Occupational Safety and Health
Under the vision of 'Creating a Safe Steelworks Lasting 100 Years', Hyundai Steel aims to 'Build a Workplace with Zero Industrial Accident'. For this, we have established health and safety policies, which are applied obligatory to all employees in the workplace. Along with, we are implementing various measures to prevent accidents and strengthen our safety capabilities.
Safety management goals and policies
Occupational Safety and Health Policy
2022 Safety Management Goals and Policies
Lasting a Century
Zero Industrial Accident
Safety and Health Policy
- 1. Establish an effective safety and health management system by prioritizing safety and health across all business operations.
- 2. Set safety and health goals and specific targets related to safety and health policies and implement action plans.
- 3. Enhance the safety and health management capabilities of employees through education and training.
- 4. Strictly comply with laws and regulations on safety and health, and the requirements of the safety and health management system.
- 5. Evaluate effectiveness and make continuous improvements through company-wide participation.
Key directions for 2022
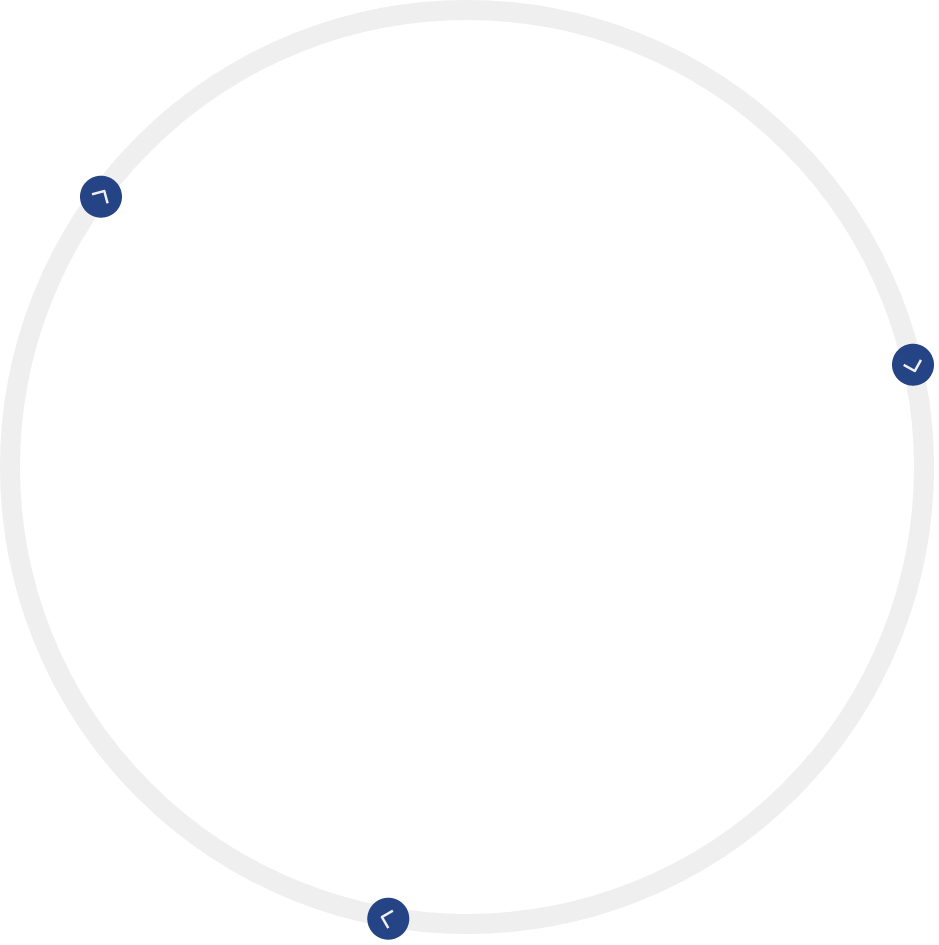
-
Reinforce the safety
and health system- - Enhance compliance with safety and health laws
- - Reduce disasters caused by unsafe behaviors
-
Legal Compliance/response
- · Responding to the Major Disaster Penalty Act
and checking the actual conditions of implementation - · Improve the safety and health system
by receiving consulting from a specialized institution
- · Responding to the Major Disaster Penalty Act
-
Win-win activities for safety and health
- · Improve the supplier selection process
- · Increase support for suppliers' safety
and health management
-
Reduction of unsafe behaviors
- · Conduct behavior-based safety inspections
- · Reinforce safety evaluation based on leading indicators
-
Improve health and safety
- - Establish a safety culture through labor-management partnership
-
Individual workers
- · Increase reward / penalty
- · Promote the safety suggestion system
and the exercise of the right to suspend work
-
Organizational perspective
- · Conduct safety awareness surveys
and hold safety workshops - · Nurture safety and health experts
and operate programs to enhance
safety awareness by hierarchy
- · Conduct safety awareness surveys
-
Support for safety and health
- · Operate a psychological safety and health program
- · Expand safety and health infrastructure
-
Lay a foundation for
a smart and safe workplace- - Reduce hazards associated with high-risk work
-
Establishment of safety investment strategy
-
· Establish a smart safety management system,
improve work procedures,
and reinforce safety systems
-
· Establish a smart safety management system,
-
Prior detection
- · Check the utilization
of wearable equipment
- · Check the utilization
-
Automation
- · Access control for using intelligent
CCTV/Radar/LiDAR
- · Access control for using intelligent
-
Unmanned equipment
- · Utilize quadruped walking robots and safety balls
for high-risk tasks (instead of workers)
- · Utilize quadruped walking robots and safety balls
Occupational Safety and Health Management System
Integrated Safety Management
Hyundai Steel operates a company-wide, integrated safety management system led by the 'Safety and Health Division' which is the control tower of our safety and health management sector that was launched in 2021. This system enables to manage more systematic and efficiently regarding safety and health issues by enhancing expertise and expediting decision making. The Safety and Health Division plays a leading role in promoting safety across the Company by establishing safety policies and regulations, enhancing safety awareness at all business sites, and efficiently operating safety systems. It also supports safety management at each business site through safety management supervision meeting, safety communication meeting, safety diagnosis and evaluation for all business sites. In addition, we have safety departments at each business site in Incheon, Pohang, Dangjin, Suncheon, and Ulsan for on-site safety management and strive to prevent safety accidents.
Safety and Health Management System Certification (ISO 45001)
Hyundai Steel set up safety management goals and carries out a set of activities, including risk assessment, safety training, and safety inspection, to achieve them. In recognition of this safety and health management system, Six business sites in Incheon, Pohang, Dangjin, Suncheon, Ulsan, and the head office have acquired ISO 45001 certification. ISO 45001 is an international standard for the safety and health management system launched in 2018 by the International Organization for Standardization(ISO) and the International Labor Organization(ILO), and is applied to all employees of the certified business sites. Moving forward, Hyundai Steel will enhance employees' awareness of the importance of safety management, optimize the safety and health management system, and strive to create an accident-free workplace with the firm belief that all accidents can be prevented.
Occupational Safety and Health Committee
The Occupational Safety and Health Act sets forth standards for occupational safety and health, and aims to prevent occupational accidents by clarifying responsibilities and promote safety and health by fostering a pleasant work environment. In line with that, Hyundai Steel operates the Occupational Safety and Health Committee across all business sites, including the Dangjin Integrated Steelworks, the cold rolling mill in Dangjin, and our steelworks in Incheon, Pohang, and Suncheon to deliberate and decide on important matters related to safety and health. The Committee includes equal number of members from both the labor and the management respectively, and meets once every quarter. Through this Committee, the labor and the management discuss and make decisions on matters relating to setting up occupational accident prevention plans, and the inspection and improvement of the work environment.
Operation of Safety, Health and Environment Advisory Committee
The Safety, Health and Environment Advisory Committee was launched in 2019 for the purpose of improving our systems and addressing on-site risk factors in the fields of safety, health, and environment by drawing on professional advice. The Committee consists of the policy advisory sector to improve systems and policies as well as discuss major issues, the technical advisory sector that reduces work-related risks and improves the work environment through on-site diagnosis together with the objective opinions from experts. In 2021, objective opinions were collected from 10 experts on major issues of the Company, such as safety management and carbon neutrality. While the spread of COVID-19 put some constraints on its activities, the Committee has continued operation and sought experts' advice through video conferences and written consultations.
Safety Management
Hyundai Steel holds regular the safety management supervision meetings led by the Chief Safety Officer(CSO). In these meetings, senior safety managers of each business site and organization decide on safety policies, and share plans and performances. We also conduct on-site inspections by the management. Through a series of inspections of all business sites, the CSO examines hazardous facilities that need improvement and visits employees on-site to give them encouragement and emphasize compliance with work procedures and safe work.
Occupational Safety and Health Diagnosis
Safety Culture Diagnosis
Hyundai Steel conducted a safety culture diagnosis aligned with on-site safety workshops in order to gauge the safety awareness of its employees and set safety management goals and directions accordingly. First, offline safety culture surveys were conducted on all employees of the Company, subsidiaries, and suppliers. Survey questions were different between managers and non-managers so as to collect more detailed information by respondent group. Survey results were used as basic data for the safety workshops and the evaluation of safety and health activities. Second, interviews were conducted both online and offline, for employees, subsidiaries, and suppliers, to discern different perspectives regarding safety awareness, and accordingly provided customized safety counseling. The safety workshops included group discussions and safety coaching, based on the survey results and actual cases of safety accidents. The safety workshops targets organizations that has a low level of safety awareness and those selected by the heads of business divisions. Based on the results of the workshops, we established a safety management reinforcement plan and carried out improvement measures.
Diagnosis and Improvement of Health and Safety System
For the purpose of improving safety management and removing legal risks, Hyundai Steel works with a specialized consulting agency to improve our safety and health systems and safety culture. As a move to reinforce the safety and health management system across all business sites including the head office, we are conducting a diagnosis on six items in two areas: safety · health system and safety culture. First, we analyzed major disaster cases, verified the adequacy of our current prevention measures and reviewed the direction of setting a major disasters prevention system. Second, we are taking consulting service to develop a compliance checklist and examine our compliance with safety laws and regulations. The Company will carry out inspections across all business divisions in phases and monitor progress on improvement until December 2020. Moving forward, Hyundai Steel will continue to work with specialized consulting agencies for safety culture diagnosis, risk assessment and safety consulting, occupational disease and work environment improvement, and advancement of safety observation.
Activities to Promote Occupational Safety and Health
Company-wide Safety Inspection
Hyundai Steel carries out company-wide safety inspections in order to discover and remove potential risks in the fields. Employees of all departments including production, maintenance, support, safety participates in the safety inspection. Regarding risks found during the inspection, countermeasures are prepared, by reflecting opinions from the fields, and progress is monitored through a computerized system. Through this company-wide safety inspection, involving all members of the Company, we strive to ensure all employees feel responsibility for safety and try to protect one another as colleagues with a sense of making a safe community.
Establishing a Process for Rapid Safety Improvement
Hyundai Steel maintains safety improvement processes in order to immediately address any risks that may occur. We work with specialized agencies to inspect our gas facilities and all hazardous machines and equipment on a regular basis. If any signs of danger, such as gas leaks, are detected during these inspections, specialists take immediate actions to address the issues. Further, if any risks are identified in our equipment, or there are safety facilities that require investment, the relevant issues are reported through our Emergency Safety Investment System, in which immediate action is taken by the maintenance department to address the issue. Hyundai Steel is fully committed to establishing safety infrastructures to protect everyone working at our business sites.
Safety Management Focusing on Prevention
We are raising our safety management standards and building a practical and effective accident-prevention system by taking action with a focus on prevention. We set safety management indicators and evaluation criteria for each organization with the goal of achieving zero industrial accidents. Safety activities which need to be implemented to prevent accidents are managed as leading indicators, such as safety inspections, addressing onsite risks, activities to enhance safety mindset, risk assessment, and the completion of safety training. After evaluation of progress made based on these indicators by the end of the year, organizations and individuals with outstanding performance are rewarded.
Company-wide Risk Assessment
Hyundai Steel conducts company-wide risk assessment every year to discover risk factors in the fields and eliminate potential risks. Risk factors identified during the assessment are removed through improvement measures established accordingly. In addition, we strive to enhance the safety awareness of employees, by sharing best practices for risk assessment improvement and using risk assessment data in regular safety training courses.
Work Environment Management
In accordance with the Occupational Safety and Health Act, Hyundai Steel measures and evaluates exposure to hazardous factors in our business sites at least once every six months by an outside agency designated by the Ministry of Employment and Labor, and reports the results to the Ministry. Accordingly, the labor-management joint evaluation team selects a specialized agency after through consultations at the Occupational Safety and Health Committee. After an on-site briefing by the agency, exposure measuring activities begin with the presence of the safety and health department, the labor union, on-site safety managers and department heads. We take measures to reduce hazardous factors based on the measurement and, as such, strive to foster a pleasant work environment.
Safe Work Environment
Hyundai Steel makes a wide range of efforts to create a safe workplace. For instance, we established and abide by work procedures and safety standards putting safety first for jobs conducted at risk-prone facilities such as oxygen facilities or facilities storing or using gas. We also conduct continuous inspection and improvement for facilities. In addition, we abide to work procedures tailored customized for the operating environment that requires processes with high temperature and pressure, and strictly manage access to risk-prone areas in order to prevent safety accidents.
Emergency Response Training and Simulation training
Hyundai Steel establishes plans to prepare for and respond to safety and health emergencies at all business sites and conducts training and simulation drills more than once a quarter in preparation for safety accidents, fires, explosions, etc. in order to promptly cope with emergencies. In an emergency, each department head takes immediate action to remove the cause of accident according to the emergency response procedures and the head of the safety and health department oversees the entire site, including on-site command and relief for the injured, so as to contain the emergency. After the emergency is resolved, a recovery plan is established, including facilities restoration, and the emergency response procedure and recurrence prevention measures are reviewed, so that we can maintain an effective emergency response system.
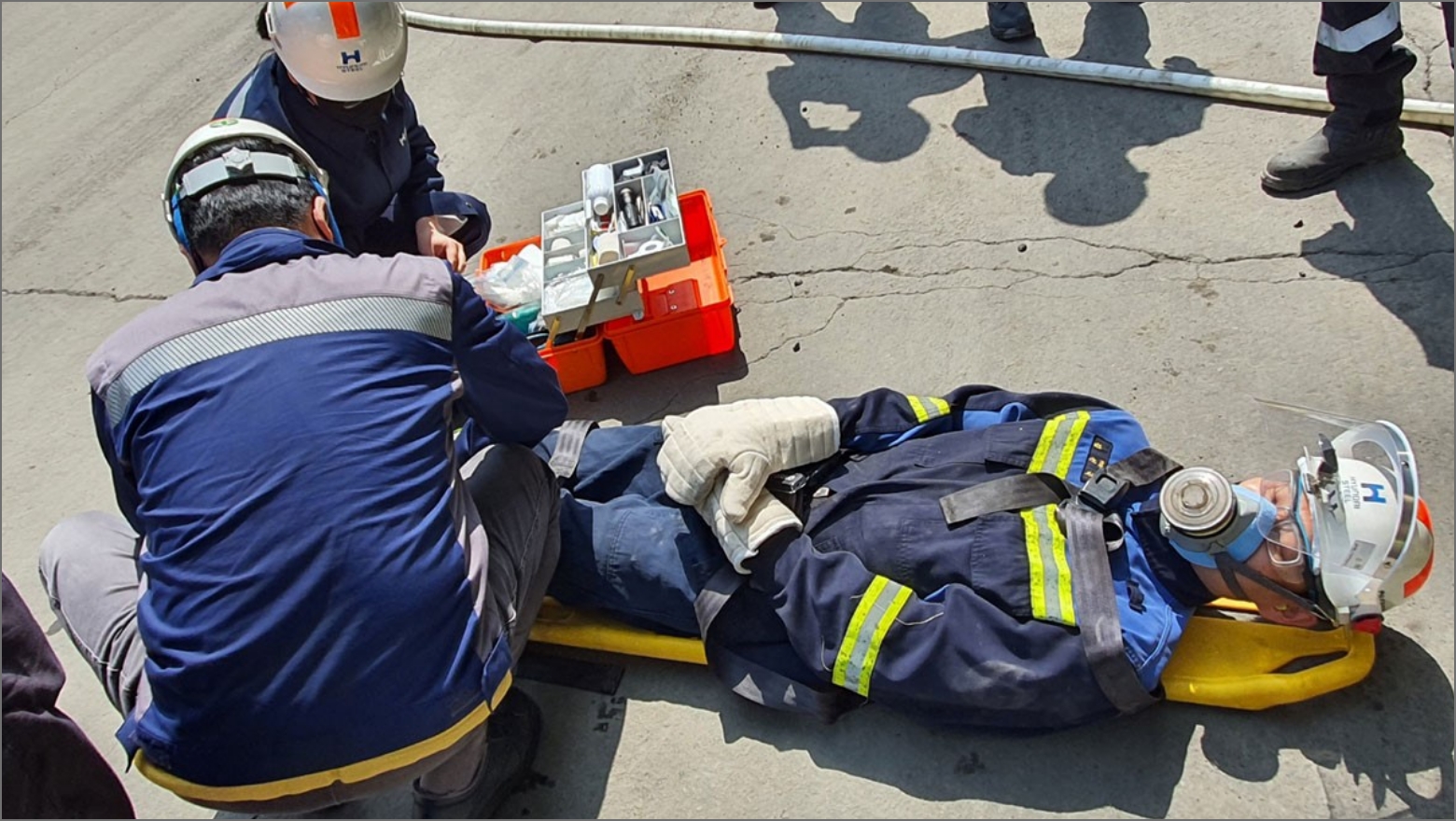
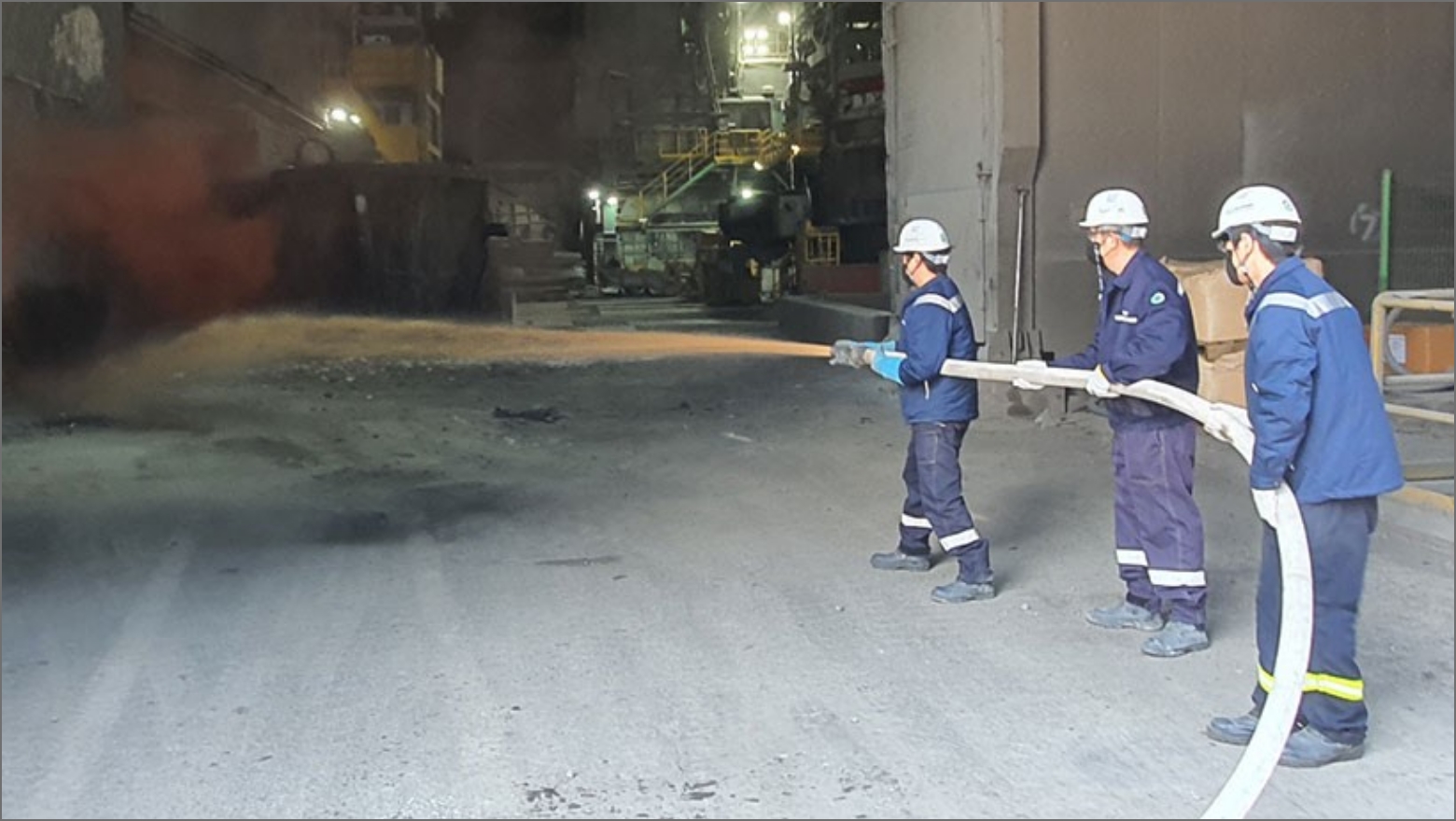
Improvement of Occupational Safety and Health
Safety Suggestion System
Hyundai Steel operates a safety suggestion system for the purpose of quickly discovering and improving risk factors in the workplace. This system is open to all workers of the Company, subsidiaries, suppliers, and outsourcing companies so that the Company can collect opinions of all members and establish countermeasures. Through such channels as "Safety Keeper", where safety status can be checked via intranet, and the website for safety management, they can easily submit suggestions for safety improvement, such as installation of safety facilities, change of work procedures, improvement of work environment, and cleaning-up. Suggestions are followed up by improvement plans, and departments in charge of safety facilities repair and maintenance take improvement measures. Progresses on the suggestions are notified through the suggestion system and SNS to those who made the suggestions. Also various measures are taken to invigorate the suggestion system, such as adding/deducting points in safety evaluation, and rewarding employees with the best/most suggestions. Moving forward, the Company will continue to listen to voices from the fields and preemptively create a safe work environment.
Safety Suggestion System

Right to Suspend Work
Hyundai Steel has introduced the "Right to Suspend Work" for the purpose to protect lives of workers in emergency and to prevent safety accidents. Upon finding an immediate danger, anyone at our business sites, including employees of the Company, subsidiaries, suppliers, and outsourcing companies, can stop work and call for safety measures in the following four steps; 1) evacuate from the site and suspend work, 2) check the site(by the supervisor of a responsible department), 3) take safety measures to remove the risk factor, 4) check the safety measures and hold a briefing session for workers(by the safety department), and resume work. The Company provides cascade training in order to internalize the right to suspend work and will continue diversified efforts to guarantee the right to safety and prevent accidents.
Company-wide Safety Management
In the event of a safety accident, Hyundai Steel strives to minimize damages and at the same time makes its best effort to prevent recurrence by promptly identifying the cause of the accident and implementing countermeasures. When a safety accident occurs, an investigation committee is formed promptly, to start investigating, identify the cause, and prepare preventive measures along with implementation plans, which are shared with all employees, and monitor progress on the measures so as to ensure safety accidents do not recur.
Accident Management Process
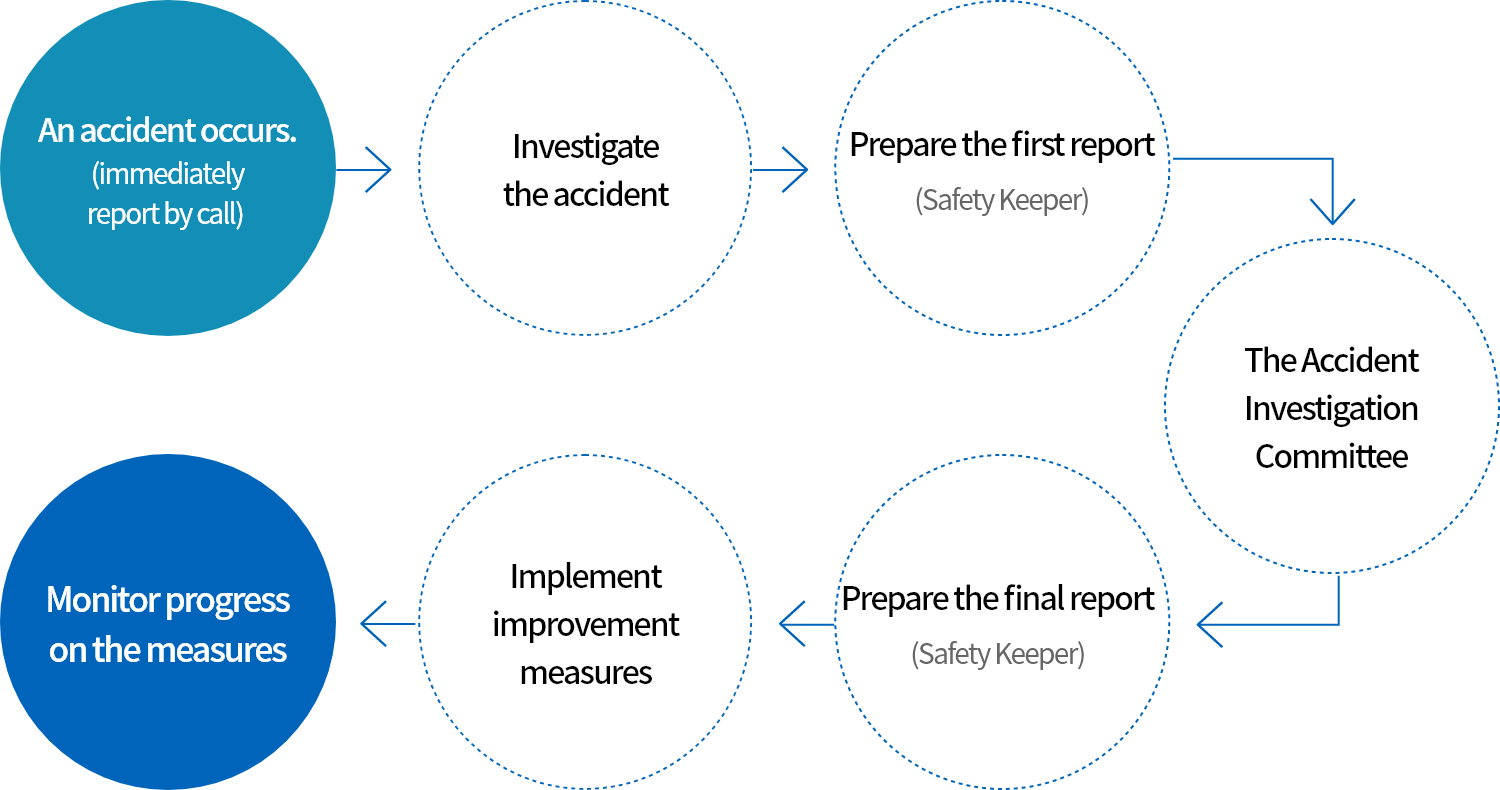
Promotion of the Safety Exchange Meeting
As a move to share issues and best practices of safety and health management within the industry, Hyundai Steel holds safety exchange meetings with companies with outstanding safety and health management and industry peers from home and abroad. Through these meetings, we expect to further enhance our safety and health management system by benchmarking best practices, such as preliminary safety review before the introduction of major facilities and risk mitigation measures for similar processes.
Occupational Safety and Health Education
Effective Safety Education
Due to the COVID-19 pandemic, Hyundai Steel has developed online courses for mandatory safety education, including basic courses, in addition to the existing offline courses. Experts provide on-site safety training in order to improve the quality of safety education at our business sites. The Company makes efforts to enhance the safety capacity of our employees by improving training facilities of the centennial safety culture center in the Dangjin Integrated Steelworks developing new training courses, and provides optimized safety education to on-site safety supervisors so that they can improve the level of safety control and play the role of a safety leader.
Safety Activities by Leaders
At Hyundai Steel, safety activities by leaders are used as a means to promote a culture of safety and spread our commitment to safety as the first priority. Through our safety program for leaders, called 'Leader's Contact', we assign monthly safety activity targets to managers, who will then conduct such safety activities as Tool Box Meetings, safety training and safety roundtables with employees in the fields.
Employee Health Promotion
Operation of Diverse Health Facilities
Hyundai Steel operate in-house clinics, psychological counseling centers, and oriental medicine treatment facilities in order to provide our employees with access to diagnoses and treatments by medical professionals. We have also put in place clinical pathology laboratories, exercise facilities and physical therapy centers - all under an advanced healthcare system. Additionally, we offer health improvement programs, such as hearing care, to employees suspected of having a disease, and are making continuous improvements to prevent additional patients as part of our efforts to manage employees' health indicators.
Supporting Physical Examination
Hyundai Steel provides physical examination to employees and their families for early detection and prevention of diseases. In addition, Hyundai Steel strives to promote the health of executives and employees by providing a wide range of health facilities and management systems at each business site.
Trauma Treatment Program
Hyundai Steel operates a trauma treatment program to prevent secondary safety accidents and psychological hazards, such as post-traumatic stress, of employees who were directly or indirectly exposed to disasters. Our in-house psychological counseling center conducts an incident impact test, provides counseling and treatment customized to employees given their level of risk, and, when necessary, offers active treatment support in partnership specialized institutions to help them overcome trauma.
Musculoskeletal Disease Prevention Program
In 2021, Hyundai Steel analyzed hazards associated with musculoskeletal impact by working with specialized agencies and introduced a program to prevent musculoskeletal diseases. Supervisors were provided with training courses on prevention of musculoskeletal disease and employees who need medical care receive treatment by medical professionals on a regular basis.
Occupational Safety and Health for Partners
Safety Management of Suppliers
To ensure safety in our steelworks, Hyundai Steel continues to engage in 'Safety Partnership' with its suppliers. With our suppliers, we share information about the safety accidents that have occurred in order to improve safety. Through monthly meetings held by Health and Safety Council, we discuss measures to address safety issues. In addition, we provide a range of training courses to support our suppliers, such as risk assessment course to the employees of suppliers, basic safety course to workers new to our business sites, and on-site safety training to strengthen expertise in safety. Furthermore, together with our suppliers, we promote safety awareness, self-directed safety culture, and ensure together that our steelworks are accident-free.
Support Safety and Health Management of Suppliers
Hyundai Steel strives to implement win-win safety management by supporting its suppliers with safety and health management and create a safety accident prevention system. We provide continuous infrastructure support, such as safety training and reinforcing management/construction of resting/sanitation facilities, along with cost support for the recruitment of safety personnel. Our efforts will be continued to foster a safe and reliable work environment for all workers partnering with us.