Energy Management
Hyundai Steel efficiently uses and manages energy by developing technologies taking into account the environmental characteristics of the energy-intensive steel industry, and strives to reduce greenhouse gas emissions.
Company-wide Activities to Reduce Energy Intensity
Hyundai Steel spends KRW 1.8 trillion in annual energy costs, and focuses its efforts on managing company-wide energy consumption and energy intensity, so as to decrease energy costs and GHG emissions. In the second half of every year, we establish an energy intensity reduction plan aligned with the production plan for the following year, and develop energy-saving tasks to achieve it. Energy managers in the fields gather for a company-wide energy meeting once a month to share and manage progress on these tasks and energy saving result.
In 2021, 64 tasks were implemented to lower energy intensity, and KRW 9.2 billion was invested in 18 tasks. With that, the Company expects to gain economic effects worth KRW 22 billion out of 23 electricity saving tasks, such as basic electricity rate reduction and introduction of tunable diode laser spectroscopy(TDLS) to the hot-rolling process, KRW 4.8 billion out of 16 by-product gas reduction tasks, including replacement of the heat recovery system for hot stoves and introduction of TDLS to heating furnaces, and KRW 3.3 billion out of 12 LNG reduction tasks, including Tundish preheating pattern improvement and heat recovery from heating furnaces.
Cost savings
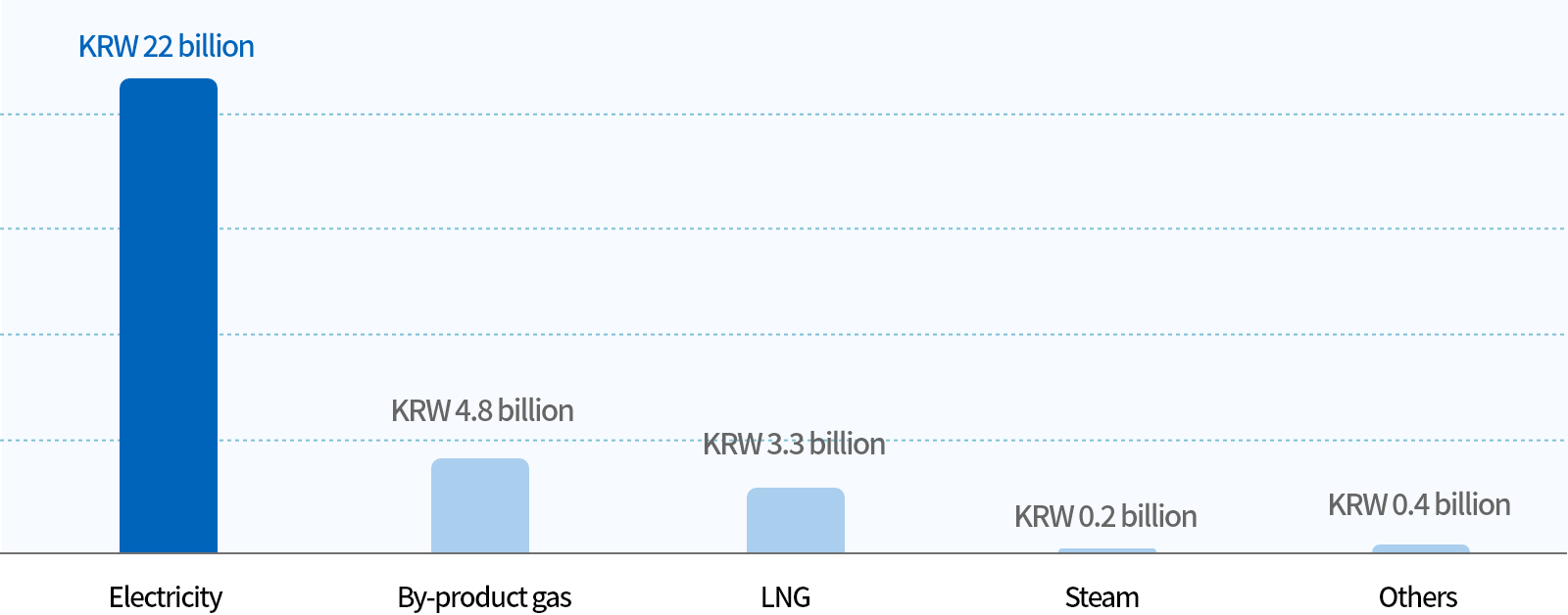
Introduction of Automatic Combustion Control System for Hot Blast Stove
A hot blast stove is a high fuel-consuming and CO2-emitting facility, which Hyundai Steel is automating its combustion process in phases to improve efficiency. We developed a system to automatically control fuel amount to hot blast stove supplying hot air suitable for blast furnace from 2018 to 2019, and applied it to all three blast furnaces from 2019 to 2021. We also developed an automatic tuning system for control models in 2021 to improve the compatibility of fuel quantity control, and applied it to #2 blast furnace. We are planning to apply the system to #1 and #3 blast furnaces in 2022, and will develop an automatic combustion air control system to improve combustion efficiency.
Hot blast stoves have a facility recovering sensible heat from off-gas, which is divided into sections for air and fuel. Flue gas generated from a hot blast stove flows into both the air and the fuel sections and preheats air and fuel for combustion. The Company optimized the division of flue gas flows between the two sections from 2019 to 2021, in order to increase heat recovery. Through automation of combustion control and improvement of heat recovery, we expect to save by-product gas costs by KRW 2.3 billion and reduce CO2 by 18,000 tons per year.
Energy Efficiency Improvement of Heating
Hyundai Steel continues to improve energy efficiency to reduce energy consumption and greenhouse gas. In particular, the furnaces heating raw materials before rolling consume a lot of fuel and emit considerable GHG, and hence we strive to improve their fuel efficiency and recover heat. Our heating furnaces for rolling are aging and we replace them by burners and facilities recovering heat from cooling water, in order to reduce energy consumption and air pollution, instead of general facilities in kind.
Regenerative Burner
Hyundai Steel has replaced heating furnaces for large-scale rolling with low-NOx regenerative burners and general burners, and improved the combustion control system. With that, the Company has complied with the Special Act on Air Quality Improvement, reduced energy intensity of LNG by more than 5%, and we expect to reduce 4.3 tons of GHG emission annually.
Introduction of Heat Recovery System for Cooling Water in Heating Furnaces
Hyundai Steel introduced a system to recover heat from cooling water in heating furnaces in 2020 and, after stabilization, the system has been in normal operation since July 2021. This system is expected to supply about 50,000 tons of steam to the local community every year by recovering the heat lost from cooling water in heating furnaces and generate annual revenue of KRW 1 billion.
Improvement of Combustion Pattern of Tundish Preheater for Continuous Casting
Hyundai Steel improved the combustion pattern of the tundish preheater in order to decrease fuel and utility costs. In the tundish, molten steel supplied from the ladle is poured into a mold for casting, and it needs preheating to a certain degree to prevent the temperature drop of the molten steel and ensure safe pouring. As a move to cut the preheating time of the tundish, we optimized set values of fuel consumption, oxygen enrichment rate, and excess air ratio for its preheater, and applied an improved consumption pattern to the facility. As a result, the average preheating time was reduced by 1.64 hours/cycle and annual LNG costs was saved about KRW 220 million.
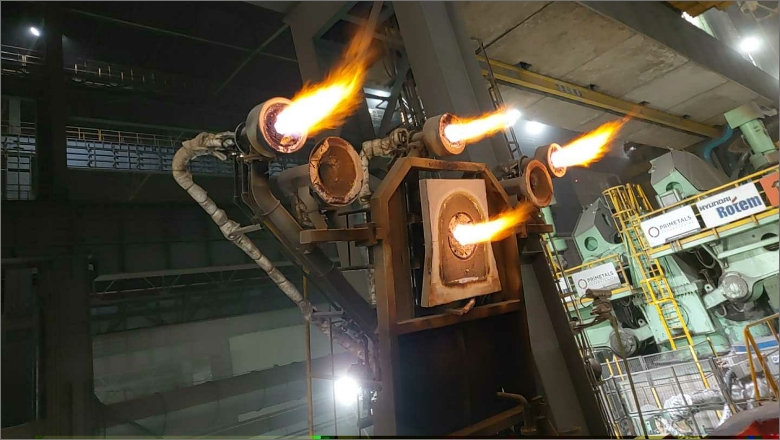
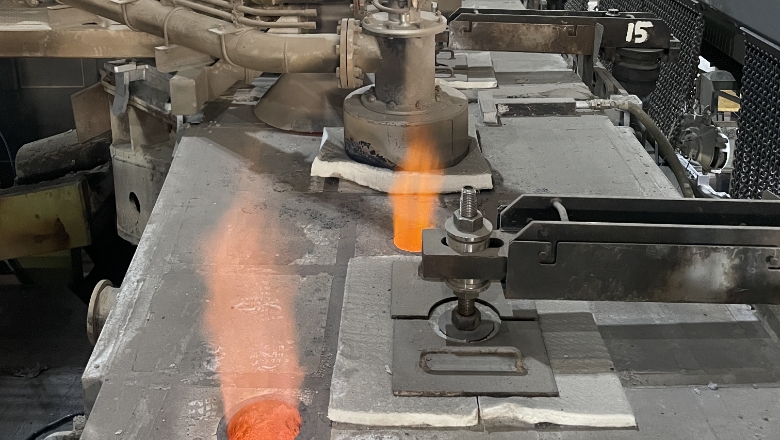
Precision Diagnosis of Steam Facilities in Dangjin Integrated Steelworks
The Dangjin Integrated Steelworks consumes 300 tons of steam per hour in the manufacturing process, of which 100 tons are supplied from our in-house power plant. If we can reduce steam consumption in the manufacturing process, the steam saved accordingly in the power plant can be used for power generation and help to reduce electricity purchase from the national power grid managed by KEPCO.
From September to November of 2021, the Company conducted a precision diagnosis by hiring a specialized agency to find ways to save steam consumption. We created a waste heat map by identifying areas to improve regarding facilities that produce or use steam across all processes, diagnose pipe traps, and investigate unused waste heat. Through this diagnosis, 13 steam reduction tasks were derived, some of which were reflected in the energy reduction tasks for 2022.
Among them, 3 tasks--optimizing steam accumulators for steel making, increasing steam production by sinter boilers, and optimizing pressure of common stand—are expected to increase electricity production by 13,500 MWh and save costs of KRW 900 million per year.
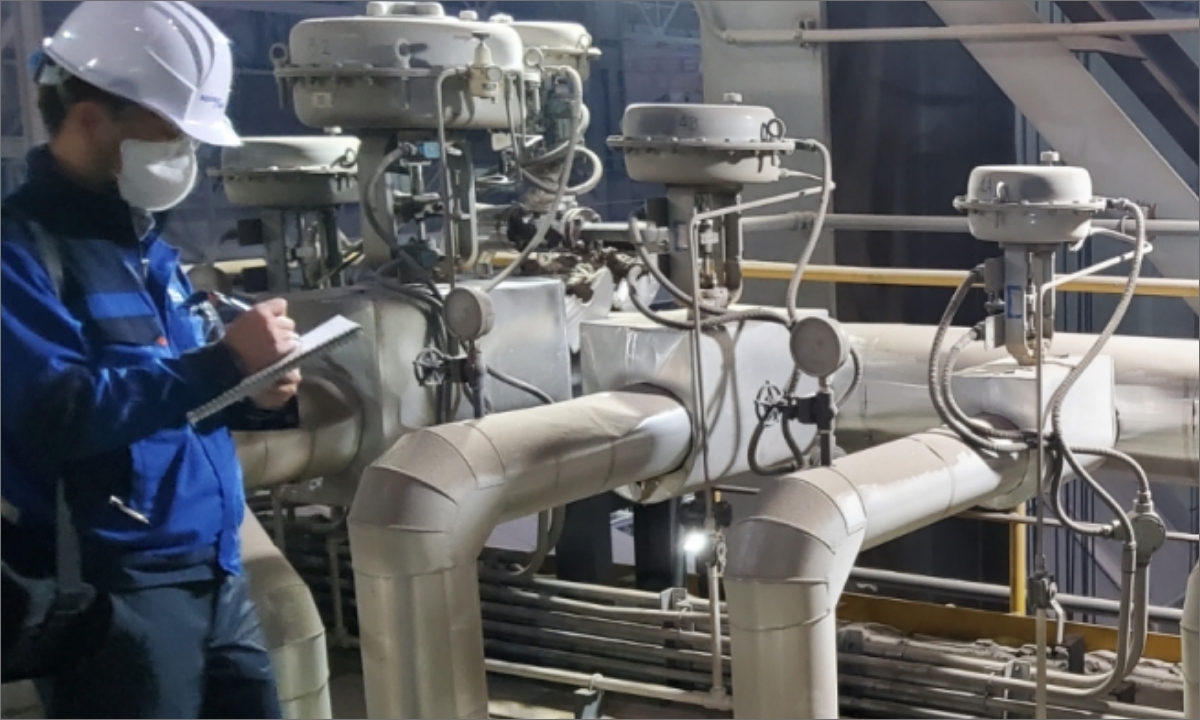